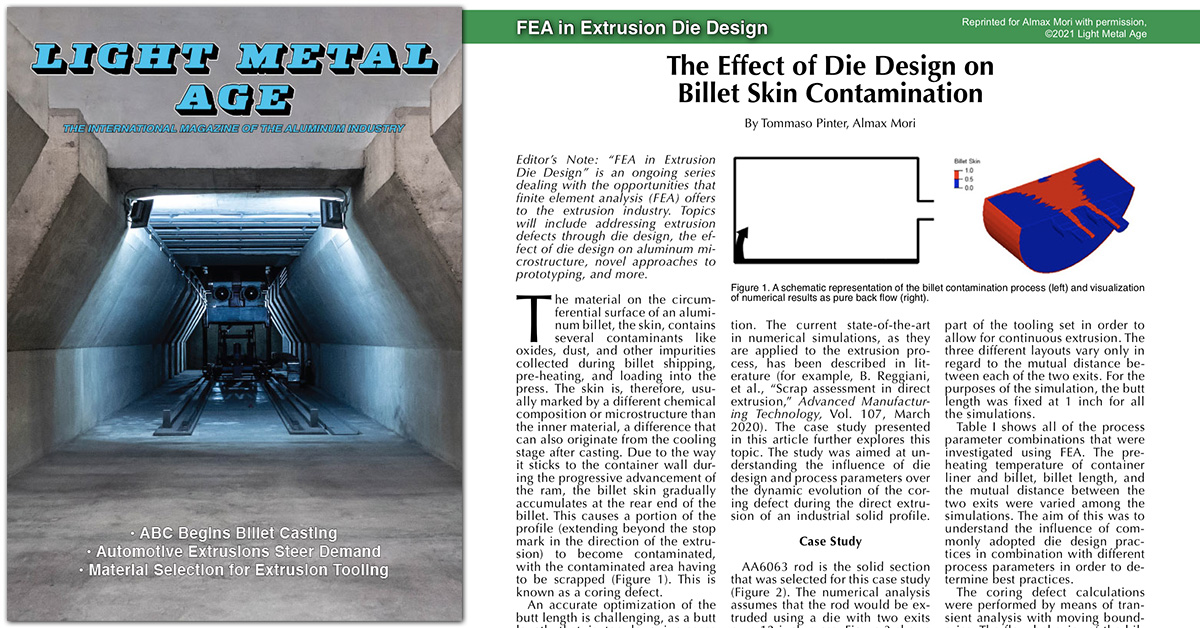
The Effect of Die Design on Billet Skin Contamination
Abstract
The material on the circumferential surface of an aluminum billet, the skin, contains several contaminants like oxides, dust, and other impurities collected during billet shipping, pre-heating, and loading into the press. The skin is, therefore, usually marked by a different chemical composition or microstructure than the inner material, a difference that can also originate from the cooling stage after casting. Due to the way it sticks to the container wall during the progressive advancement of the ram, the billet skin gradually accumulates at the rear end of the billet. This causes a portion of the profile (extending beyond the stop mark in the direction of the extrusion) to become contaminated, with the contaminated area having to be scrapped. This is known as a coring defect. The case study presented in this article further explores this topic. The study was aimed at understanding the influence of die design and process parameters over the dynamic evolution of the coring defect during the direct extrusion of an industrial solid profile.